Aeroglide Dryer Model C1 120-65 RGC
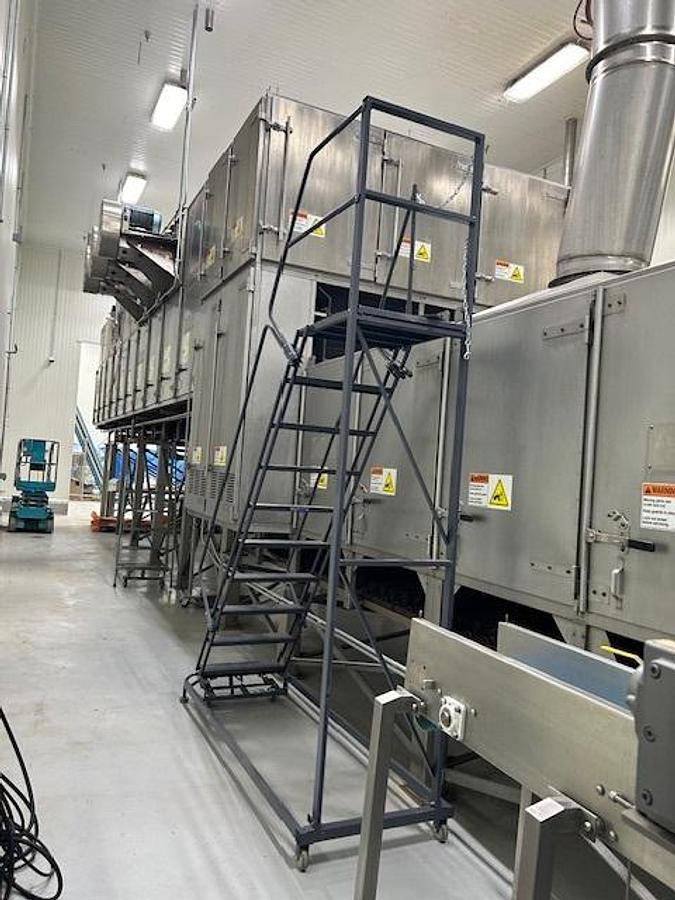
Aeroglide Dryer Model C1 120-65 RGC
Contact us for price
Location:United States
Description
Aeroglide Dryer
Model C1 120-65 RGC, Ser# 05153-02, Mfg. 2005, Natural Gas,
Overall Dimensions: 65' 2'' Length, Width (Frame) 15' 8'', Height (Including Legs) 15' 4''
Bed Width 9' 9'', Drying Bed Area 350 Ft.2, Cooling Bed Area 140 Ft.2
Product Description: Last used on Coated Almond Accents & Almond Products
Last used in 2024.
Dryer was rebuilt and last used for snack foods!
Contact us for a quote!
Dryer is currently dismantled and in a storage facility in Chicago area!
COOLING:
Number of Cooling Zones: 1, Location of Cooling Zone: Extended
Airflow Direction: Drying Zone 1 Reversible Up/Down-Flow
Drying Zone 2 Reversible Up/Down-Flow
Cooling Zone Up-Flow
NO CONTROLS (*See Rebuild below for New Panel)
NO LEGS (*New Ones on Rebuild)
NO EXHAUST FANS, NO CHIMNEYS & NO FRESH AIR DUCT BROUGHT IN (*Erie to Provide) REFURBISH DESCRIPTION:
Full description and list of work done below!!!!
A. STAINLESS STEEL BASE OF INFEED/TENSION SECTION OF OVEN AND RECONDITIONING:
WORK ON INFEED:
• DISASSEMBLE AND CLEAN AND BUFF
• FIX BENT PARTS
• NEW TENSION CHAIN AND SPRINGS MATERIAL:
• 4 FEET STRUCUTRE LEGS OF HSS 6”X6” X ¼”
• 2 SECTIONS OF 2” X2” X ¼” X 20’ ANGLE
• 3” X 3” TABS MADE FROM 3” X3/8” THICK X 18 ‘ LONG METAL
• 9” X 9” X3/8” MOUNTING PLATES MAD FROM 10 ‘ OF METAL LABOR:
• DRILLING AND THREADING 9” X 9” PLATES
• DRILLING THREADING 3” X 3” PLATES
• PUNCHIN HOLES ON 3” X 3” PLATES
• CUTTING AND PUNCHIN HOLE SIN 2” X 2” ANGLE
• WATER JET CUTTING PLATES
• WELDING 288 INCHES OF STAINLESS TIG
• CUTTING 6” X 6” HSS TUBING
• BUFFING PARTS
B. 40’ HEATING SECTION OF OVEN BASE STRUCTURE RECONDITIONING:
MATERIAL:
• 5 ’ PIECES FEET STRUCUTRE LEGS OF HSS 6”X6” X ¼” 20’
• 21 PIECES OF 2” X2” X ¼” X 20’ ANGLE
• 2 PIECES OF 20’ X 3” X 3” TABS MADE FROM 3” X3/8” THICK
• 9” X 9” X3/8” MOUNTING PLATES MAD FROM 10 ‘ OF METAL PLATE X 48” LABOR:
- DRILLING AND THREADING 9” X 9” PLATES
- DRILLING THREADING 3” X 3” PLATES
- PUNCHIN HOLES ON 3” X 3” PLATES
- CUTTING AND PUNCHIN HOLE SIN 2” X 2” ANGLE
- WELDING 960 INCHES OF STAINLESS TIG
- WATER JET CUTTING PLATES
- CUTTING 6” X 6” HSS TUBING
- BUFFING PARTS
C. OVEN SECTION OF CEREAL AFTER BAKING , FLIPPING TO COOLER SECTION:
MATERIAL:
• 8 FEET STRUCUTRE LEGS OF HSS 6”X6” X ¼” X 20’
• 10 SECTIONS OF 2” X2” X ¼” X 20 ‘ ANGLE
• 3” X 3” TABS MADE FROM 3” X3/8” THICK X 20‘ LONG METAL
• 9” X 9” X3/8” MOUNTING PLATES MAD FROM 7‘ OF METAL LABOR:
• DRILLING AND THREADING 9” X 9” PLATES
• DRILLING THREADING 3” X 3” PLATES
• PUNCHING HOLES ON 3” X 3” PLATES
• CUTTING AND PUNCHIN HOLE SIN 2” X 2” ANGLE
• WATER JET CUTTING PLATES
• WELDING 288 INCHES OF STAINLESS TIG
• CUTTING 6” X 6” HSS TUBING
• BUFFING PARTS
D. COOLING SECTIONS OF OVEN (14’2’ LONG ) BUILD , FEET BASES AND REPAIR OF ONE CHAMBER AT SHOP:
MATERIAL:
• 6 STRUCTURE LEGS OF HSS 6”X6” X ¼” X 13’’
• 10 SECTIONS OF 2” X2” X ¼” X 20 ‘ ANGLE
• 3” X 3” TABS MADE FROM 3” X3/8” THICK X 20‘ LONG METAL
• 9” X 9” X3/8” MOUNTING PLATES MAD FROM 7‘ OF METAL
• 4 X 48” X 10’ 12 GUAGE STAINLESS STEEL SHEETS LABOR:
• DRILLING AND THREADING 9” X 9” PLATES
• DRILLING THREADING 3” X 3” PLATES
• PUNCHIN HOLES ON 3” X 3” PLATES
• CUTTING AND PUNCHIN HOLE SIN 2” X 2” ANGLE
• WATER JET CUTTING PLATES
• BREAK SHEAR DUCTS MISSING FOR AIR INTAKE CONNECITONS AND EXHAUST CONNECTION
• WELDING 610 INCHES OF STAINLESS TIG
• CUTTING 6” X 6” HSS TUBING
• BUFFING PARTS
D. OVEN OUT FEED WITH GRANULATOR/BREAKER AND DRIVE MOTOR LEGS SUPPORT STRUCTURE AND ONE COOLING SECTION REPAIR:
MATERIAL:
• 4 STRUCTURE LEGS OF HSS 6”X6” X ¼” X 8’ ’’
• 8 SECTIONS OF 2” X2” X ¼” X 20 ‘ ANGLE
• 3” X 3” TABS MADE FROM 3” X3/8” THICK X 15‘ LONG METAL
• 9” X 9” X3/8” MOUNTING PLATES MAD FROM 3’ X 48’ ‘ OF METAL
• 4 X 48” X 10’ 12 GUAGE STAINLESS STEEL SHEET LABOR:
• DRILLING AND THREADING 9” X 9” PLATES
• DRILLING THREADING 3” X 3” PLATES
• PUNCHIN HOLES ON 3” X 3” PLATES
• CUTTING AND PUNCHIN HOLE SIN 2” X 2” ANGLE
• WATER JET CUTTING PLATES
• BREAK SHEAR DUCTS MISSING FOR AIR INTAKE CONNECTIONS AND EXHAUST CONNECTION
• WELDING 632 INCHES OF STAINLESS TIG
• CUTTING 6” X 6” HSS TUBING
• BUFFING PARTS
E. REFURBISH OF 6 HEAT BLOWER ASSEMBLIES: MATERIAL:
• 6 SHEETS 14 GUAGE STAINLESS STEEL 48” X 10’
• 12 HIGH TEMP BEARINGS MODEL P2B-SCM-208-HT
• BEARINGS FOR MOTOR REPAIRS
• REVIEW WINDINGS
• NEW GATES BELTS LABOR:
• CUT AND BREAK METAL
• WELD GUARDS
• POLISH GUARDS
• SANDBLAST MAIN BASES
• CLEAN AND SHINE SHAFTS
• BALANCE FANS
• DISARM MOTORS
• REPLACE INNER BEARINGS
• SANDBLAST BODY
• REPAINT
F. INSPECT AND UPDATE GAS TRAINS:
• DIS-ASSEMBLE AND REPAINT PIPES
• REVIEW VALVES AND SOLENOIDS TO ENSURE ARE UP TO CODE AND REPLACE IF NECESSARY
• CHECK PILOT AND SOLENOID VALVES, REPLACE IF NECESSARY\ MATERIALS & LABOR:
• PAINT
• SANDBLAST SAND
• SOLVENT
G. INSPECT AND RECONDITION ECLIPSE BURNERS:
• DIS-ASSEMBLE AND REPAINT
• REVIEW VALVES AND SOLENOIDS TO ENSURE ARE UP TO CODE AND REPLACE IF NECESSARY
• CHECK PILOT SPARK TRANSFORMER
• CHECK HEAT SENSOR RODS
• CHECK MODUTROL
• CHECK COMBUSTION BLOWER AND REPLACE MOTOR IF DAMAGED
• CHECK ESPRIAS MATERIALS & LABOR:
• SPARK TRANSFORMER
• MODUTROL
• HEAT SENSOR RODS
• SOLENOIDS PILOT
• COMBUSTION FAN MOTORS
• COMBUSTION FILTERS
• COMBUSTION FAN BEARINGS
NEW CONTROLS:
- Temperature Controls
o All zones of the oven are individually controlled for a temperature range of 100°F to 650 °F. Each is digitally operated, which receives a signal from a thermocouple mounted in the supply air stream. This digitally controls the flame modulation to maintain the design set point temperature.
- Control Panel
o One Control Panel is provided for the system. The Panel is powder coated mild steel. The components are Allen Bradley with Eurotherm temperature controls and Siemens Flame Safeties. The unit is pre-wired and free standing, complete with burner ignition and flame parts subject to normal wear and tear. All electrical components and outside supplied parts are subject to factory warranty. Used items that have not been rebuilt or work not performed are no warranty.
Specifications
Manufacturer | Aeroglide Dryer Model C1 120-65 RGC |
Condition | Used |
Stock Number | ChicagoDryer |